Products
Contact Us
E-mail:jd319@jindesic.com
Telephone:+86-539-6261319
Address:Economic Development Zone, Linshu County, Shandong Province


Silicon carbide for ceramic membranes
Classification:
Tag:
Silicon carbide is produced by high-temperature smelting of silica and anthracite or petroleum coke in an electric furnace at 1800℃-2400℃ for 50-200 hours.
Silicon carbide has various crystal forms, with the alpha (α) phase, also known as polycrystalline silicon carbide, being primarily used for abrasives and refractory materials.
Due to its unique silicon-carbon structure, silicon carbide has a very stable chemical structure. It is resistant to oxidation, acids, bases, and corrosion, with a hardness second only to diamond (internationally, diamond is rated at Mohs hardness 10, while silicon carbide has a Mohs hardness of 9.3-9.5). It can be used for abrasives, grinding wheels, sandpaper, polishing, grinding, cutting, silicon carbide structural ceramics, refractory materials, etc. In the steelmaking process, silicon carbide can also be used as a deoxidizer for carbon and silicon, as it begins to decompose above 1300°C.
Silicon carbide is classified by color into black silicon carbide and green silicon carbide. Black silicon carbide is mainly produced from anthracite and silica (quartz sand) at high temperatures. Green silicon carbide is mainly produced from petroleum coke and silica, with a small amount of sodium chloride added, resulting in a dark green color.

Carbon ceramic membrane processing technology and equipment using silicon carbide micro powder.
The raw silicon carbide blocks are crushed by a jaw crusher and then ground into coarse particles of 5mm-0, which are then milled in a ball mill to produce fine particles of 60#-0. After magnetic separation, they undergo further processing through Raymond mills, air flow mills, etc., to produce silicon carbide particles that reach micro powder sizes of 30um to 5um, followed by air classification and screening processes, gradually producing a series of silicon carbide micro powder grades that meet industry standards or customer requirements.

Applications and advantages of silicon carbide ceramic membranes.
Silicon carbide ceramic membranes have high chemical stability, good thermal shock resistance, strong hydrophilicity, high membrane flux, high mechanical strength, concentrated pore size distribution, and a good pore structure gradient. Compared to traditional membrane materials, silicon carbide ceramic membranes can efficiently separate suspended particles and oil droplets in water without being affected by the quality of the feed water. Due to their stable and durable characteristics, they can effectively reduce downtime and installation costs, and are considered a promising new type of separation membrane that may replace various inorganic membranes.
1. High mechanical strength, resistant to high and low temperatures, high pressure (higher hardness and mechanical strength than other ceramic membranes), resistant to acids, bases, and solvents.
2. Enhanced coupling reactions, improving reaction efficiency.
3. High separation precision and recovery efficiency, especially for nano-sized catalyst particles.
4. Higher anti-pollution performance and excellent cleaning recovery.
5. Replaces traditional processes such as sedimentation, plate and frame filtration, and centrifugal separation.
6. No additives are needed; concentrated substances (mycelium, proteins, etc.) can be recovered as feed.
7. Ensures over 95% integrity and activity of the fermented microbial cells.
8. Reduces emissions, saves energy, and is environmentally friendly.
9. Simple process and short flow.
10. Low operating costs, low maintenance costs, and long service life.
Silicon carbide testing equipment for ceramic substrates.

Loading and shipping.
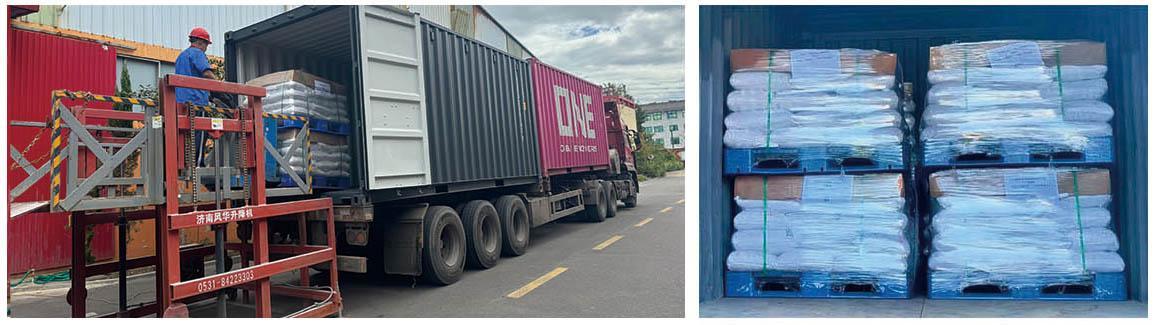