Products
Contact Us
E-mail:jd319@jindesic.com
Telephone:+86-539-6261319
Address:Economic Development Zone, Linshu County, Shandong Province


Silicon carbide for foam ceramics
Classification:
Tag:
Silicon carbide is produced by high-temperature smelting of silica and anthracite or petroleum coke in an electric furnace at 1800℃-2400℃ for 50-200 hours.
Silicon carbide has various crystal forms, with the alpha (α) phase, also known as polycrystalline silicon carbide, being primarily used for abrasives and refractory materials.
Due to its unique silicon-carbon structure, silicon carbide has a very stable chemical structure. It is resistant to oxidation, acids, bases, and corrosion, with a hardness second only to diamond (internationally, diamond is rated at 10 on the Mohs scale, while silicon carbide has a Mohs hardness of 9.3-9.5). It can be used for abrasives, grinding wheels, sandpaper, polishing, grinding, cutting, silicon carbide structural ceramics, refractory materials, etc. In the steelmaking process, silicon carbide begins to decompose above 1300°C and can also be used as a deoxidizer for carbon and silicon addition.
Silicon carbide is classified by color into black silicon carbide and green silicon carbide. Black silicon carbide is mainly produced from anthracite and silica (quartz sand) at high temperatures. Green silicon carbide is mainly produced from petroleum coke and silica with a small amount of sodium chloride added, resulting in a dark green color.

Silicon carbide foam ceramic processing technology and equipment
The raw silicon carbide blocks are crushed by a jaw crusher and then ground into coarse particles of 5mm-0. These are then fed into a ball mill to be ground and screened into fine particles of 60#-0. After magnetic separation, they undergo further processing through Raymond mills, air flow mills, etc., to produce silicon carbide particles that reach micro-powder sizes of 30um to 5um, followed by air classification and screening processes, gradually producing a series of silicon carbide micro-powder grades that meet industry standards or customer requirements.

Applications and advantages of silicon carbide foam ceramics
1. Lightweight characteristics: The density of foam ceramic materials typically ranges from 0.3-0.8g/cm3, significantly reducing weight compared to traditional ceramic materials, making them appear lighter.
2. High strength performance: Its unique porous structure not only increases the strength of the material but also gives it excellent compressive and bending resistance, allowing it to better withstand deformation and breakage under stress.
3. High-temperature stability: Foam ceramic materials can maintain their original structure and performance at high temperatures, making them widely applicable in high-temperature insulation fields.
4. Excellent thermal insulation performance: With its rich porous structure, foam ceramic materials effectively reduce heat conduction, achieving outstanding thermal insulation effects.
5. Excellent corrosion resistance: Foam ceramic materials exhibit outstanding corrosion resistance, meaning they can maintain stable performance in corrosive environments such as acids and bases.
Detection equipment for silicon carbide foam ceramics

Packaging
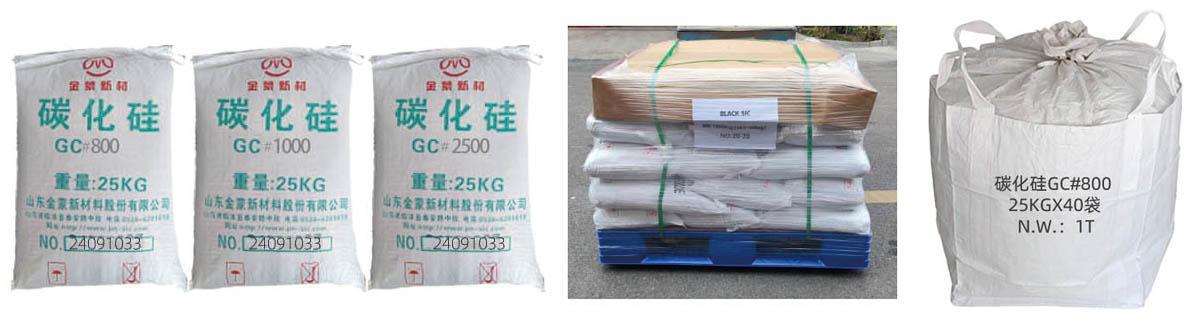
Loading and shipping
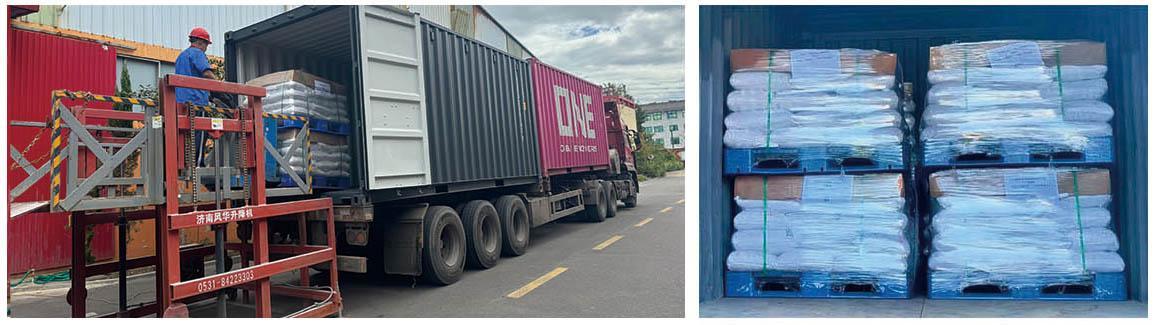