What is a microchannel reactor?
2024-12-12
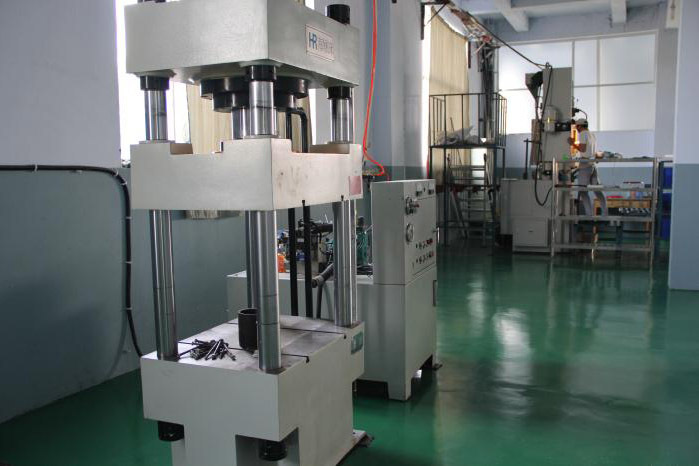
Microchannel, also known as microchannel heat exchanger, is a type of heat exchanger with a channel equivalent diameter of 10-1000μm. This type of heat exchanger has dozens of fine flow channels inside the flat tubes, which are connected to circular headers at both ends. The headers are equipped with baffles to separate the flow channels of the heat exchanger into several processes. Compared to traditional chemical production, microchannels have great development potential and broad application prospects in the field of fine chemicals. So let's understand microchannels from several aspects.
1. Understanding Microchannel Reactors
Introduction to Microchannel Reactors
Essentially, a microchannel reactor is a type of continuous flow tubular reactor. It includes mixers, heat exchangers, reactor controllers, and other components required for chemical units. Currently, the overall structure of microchannel reactors can be divided into two types: one is an integrated structure, which is manifested in the form of counterflow or crossflow heat exchangers, allowing for high flux operations in a unit volume. In the integrated structure, only one operational step can be performed at a time, and these corresponding devices are connected to form a complex system. The other is a layered structure, which consists of a stack of modules with different functions, performing one operation in one layer and another operation in another layer. The flow of fluids in each layer can be controlled by intelligent diversion devices. For higher flux, some microchannel reactors or systems are usually operated in parallel.
2. Principles of Microchannel Reactors
Microreactors mainly refer to a type of multi-channel micro-structured small reactor manufactured through micro-machining and precision technology, with channel sizes only at the sub-micron and sub-millimeter levels. In addition, because microreactors have heat transfer/mass transfer characteristics that are 1-3 orders of magnitude better than traditional chemical equipment, they are particularly suitable for experiments involving high exothermic and rapid reactions. Many people are likely interested in the principles of microreactors.
The concept of microchemical technology originates from the heat transfer mechanisms at conventional scales. For laminar flow in circular tubes, when the wall temperature is kept constant, it can be seen from formula (1) that the heat transfer coefficient h is inversely proportional to the tube diameter d, meaning that the smaller the diameter, the larger the heat transfer coefficient; for laminar flow in circular tubes, when the concentration of component A at the tube wall is kept constant, the mass transfer coefficient kc is inversely proportional to the tube diameter (formula (2)), meaning that the smaller the diameter, the larger the mass transfer coefficient. Since the flow in microchannels is mostly laminar, it mainly relies on molecular diffusion for mixing between fluids. From formula (3), it can be seen that the mixing time t is proportional to the square of the channel scale. Reducing the characteristic size of the channel not only greatly increases the specific surface area but also significantly enhances the transfer characteristics of the process.
Nu=hd/k=3.66(1)
Sh=kc/DAB=3.66(2)
t=d 2/DAB(3)
Where Nu is the Nusselt number, Sh is the Sherwood number, and D is the diffusion coefficient. The chemical reactions occurring in chemical processes are controlled by either the transfer rate or intrinsic reaction kinetics, or both. For instantaneous and rapid reactions, when conducted in traditional scale reaction equipment, they are controlled by the transfer rate, while in micro-scale reaction systems, the transfer rate is significantly increased, thus the reaction rate of such processes will be greatly enhanced; for example, the excitation state oxygen generator in oxygen-iodine chemical lasers (reaction of chlorine with hydrogen peroxide alkaline solution), and direct fluorination of hydrocarbons. Slow reactions are mainly controlled by intrinsic reaction kinetics, and one of the key means to enhance the process is to increase the intrinsic reaction rate, which can usually be achieved by raising the reaction temperature or changing the process operating conditions; while medium-speed reactions are influenced by both transfer and reaction rates, similar measures to those for slow reactions can also be taken. Currently, most industrial applications of hydrocarbon nitration reactions belong to medium-slow reaction processes, with reaction times ranging from several minutes to several hours. In microreactors, adiabatic nitration can be employed while simultaneously changing process conditions to reduce the reaction time to seconds. Therefore, theoretically, almost all reaction processes can achieve process enhancement.
3. Classification of Microchannel Reactors
Microreactors can also be divided into gas-solid catalytic microreactors, liquid-liquid phase microreactors, gas-liquid phase microreactors, and gas-liquid-solid three-phase catalytic microreactors.
1. Gas-solid catalytic microreactors are suitable for gas-solid catalytic reactions due to the characteristics of microreactors. So far, research on microreactors has mainly focused on gas-solid catalytic reactions, resulting in a variety of gas-solid catalytic microreactors. The simplest gas-solid catalytic microreactor is a microchannel with a catalyst fixed on the wall. More complex gas-solid catalytic microreactors generally couple one or more functions such as mixing, heat exchange, sensing, and separation. A widely used example is toluene gas-solid catalytic oxidation.
2. Liquid-liquid phase reactors are currently much less common compared to gas-solid catalytic microreactors. A key influencing factor for liquid-liquid phase reactions is sufficient mixing, so liquid-liquid phase microreactors are either coupled with micro-mixers or are micro-mixers themselves. There are few cases of microreactors designed specifically for liquid-liquid phase reactions that are coupled with micro-mixers and other functional units. Notable examples include the vitamin precursor synthesis microreactor designed by BASF and the microreactor designed by MIT for completing the Dushman chemical reaction.
3. Gas-liquid phase microreactors can be classified into two types: one type has gas and liquid flowing from two separate microchannels into one microchannel, forming a T-shaped structure. Due to the flow state of fluids in the gas and liquid phases being similar to that in bubble columns, typical flow patterns such as bubble flow, slug flow, annular flow, and jet flow appear with changes in gas and liquid flow rates. This type of gas-liquid phase microreactor is called a micro-bubble column. The other type is a falling film microreactor, where the liquid phase flows downward in a film-like manner, allowing for sufficient contact between the gas and liquid phases on the film surface. The reaction rate and conversion rate of gas-liquid reactions often depend on the contact area between the gas and liquid phases. Both types of gas-liquid phase reactors have a very large gas-liquid contact area, with their internal surface area approaching 20000m2/m3, which is an order of magnitude larger than that of traditional gas-liquid phase reactors.
4. Gas-liquid-solid three-phase catalytic microreactors are also quite common in chemical reactions, with many varieties. In most cases, the solid is a catalyst, while the gas and liquid are reactants or products. MIT has developed a micro-packed bed reactor for gas-liquid-solid three-phase catalytic reactions, which has a structure similar to that of fixed bed reactors, with catalyst particles packed in the reaction chamber (microchannel), and the gas and liquid phases are divided into several streams that mix in the reaction chamber for catalytic reactions.
4. Introduction to the Advantages of Microchannel Reactors
Compared to conventional reaction vessels (such as flasks), the structural characteristics of microchannel reactors determine their unique advantages, which are mainly reflected in the following aspects:
(1) Precise control of reaction temperature,
For highly exothermic reactions, if the mixing and heat transfer efficiency is not high, local overheating can easily occur. The microchannel has excellent heat transfer and mass transfer characteristics, preventing excessive accumulation of reaction temperature and allowing precise control within a certain range.
(2) Large specific surface area, high transfer rate, short contact time, and fewer by-products: The characteristic scale of microreaction channels is small, with microchannels typically ranging from 5000 to 50000 mm, significantly enhancing heat transfer and mass transfer capabilities per unit area.
(3) Rapid and direct scaling up: Traditional scaling processes involve scaling effects, where the purpose of scaling is achieved by increasing the size and scale of production equipment, which is time-consuming and labor-intensive, and cannot respond immediately to market demands, leading to delays. In contrast, the microreaction system has a multi-channel structure, where each channel acts as an independent reactor. When scaling up production, there is no need to scale up the reactor; it is sufficient to increase the number of channels in parallel, known as "number-increasing scaling."
(4) High safety: A large amount of heat can be removed in a timely manner, ensuring that the reaction temperature remains within the set range, greatly reducing the likelihood of accidents.
(5) Good operability: The microreaction system is a modular parallel system with good portability, allowing for decentralized construction and on-site production and supply at the product usage location, truly achieving the portability of chemical plants. It can also adjust production by increasing or decreasing the number of channels and replacing modules according to market conditions, providing high operational flexibility.
Due to its many advantages, the successful application of microchannel reactor technology in the chemical industry has attracted increasing attention.
5. Applicable Scope of Microchannel Reactors
We all know that microreactors have many advantages, such as excellent mass and heat transfer capabilities, which greatly reduce the likelihood of accidents; rapid and direct scaling capabilities, saving costs and time, etc. However, there are also certain limitations, and for this reason, many experiments cannot use microreactors. Therefore, it is very necessary for chemical enterprises to understand the applicable scope of microchannel reactors.
Strictly speaking, it is currently difficult to define which reactions are suitable for microchannel reactors, as the characteristics of each reaction differ, and there are many types of microchannel reactor devices. However, it is generally believed that 20-30% of existing synthetic reactions can be technically modified using microchannel reactors. Additionally, using microchannel reactors, we can implement about 20%-30% of processes previously considered dangerous. In other words, it is currently estimated that nearly 30-50% of chemical processes can be technically modified using microchannel reactors.
From a structural perspective, microchannel reactors can currently be used for the following types of reactions.
1. Reactions that are inherently fast but limited by the transfer process, resulting in a low overall reaction rate. These reactions mainly include liquid-liquid multiphase reactions, including liquid-liquid extraction and other physical processes. The characteristic of this process is that the reaction itself is fast, but the diffusion of substrates between liquid phases leads to a low overall reaction rate. In traditional reaction vessels, stirrers are generally used for reactions, which are inefficient and cannot fully achieve mixing between the two liquid phases, resulting in low reaction efficiency. In microchannel reactors, the small channel size reduces the diffusion scale, allowing these reactions to proceed rapidly.
2. Reactions that are inherently fast but vigorous, highly exothermic, and where products are easily destroyed. These reactions mainly include nitration, diazotization, and some hydrolysis and alkylation reactions. Nitration and diazotization reactions are very fast and vigorous, but in actual factory operations, the reaction time is often measured in hours. This is because the heat transfer capacity of the reaction vessel is limited, and to prevent the temperature within the system from becoming uncontrollable, reagents must be added dropwise. It can be said that the reaction speed is entirely determined by the heat transfer capacity. If a microchannel reactor with strong heat transfer capacity is used, reagents can be quickly introduced while maintaining stable reactions. This type of reaction has industrialization prospects and should be prioritized.
3. Reactions that require strict control of the flow pattern inside the reactor.
These reactions mainly include the synthesis of nanoparticles, etc. This type of process has been previously introduced, mainly utilizing the flow regularity within the microchannel to prepare materials with narrow particle distribution, thereby increasing the added value of the products. These reactions generally have low product yields but high added value; sometimes, a few experimental devices can be combined to form a production device, and the application prospects are also broad.
4. Some gas-liquid reactions can theoretically use microchannel reactors, but currently, there is no good gas-liquid reactor structure. Hydrogenation, of course, has many types; some hydrogenation reactions have high reaction rates but are limited by the diffusion of hydrogen into the liquid phase, resulting in a low overall reaction rate. In this situation, the mixing characteristics of microchannel reactors can be utilized for reactions, similar to the first type of reaction, but here the focus is on enhancing the gas-liquid mass transfer process. However, gas-liquid processes have their particularities, mainly in fluid distribution and control, which leads to the absence of suitable gas-liquid microchannel reactors for scaling up. Therefore, experimental research in this area is very active, and in industrial applications, unless the yield is small and can directly use experimental devices, there is no feasibility.
5. Reactions with particle sizes reaching more than 10% of the microchannel characteristic scale and solid content exceeding 5% should not use microchannel reactors.
6. Technical Requirements for Microchannel Reactor Systems
1. ★ Overall requirements: The synthetic reaction system includes at least 6 independently operating reactant channels.
2. ★ The reactor support can flexibly configure the number of reaction modules (no less than 4), including at least 8 feed and collection interfaces and 4 heat transfer fluid interfaces.
3. ★ The reactor can achieve two temperature zones separated by two constant temperature circulators and a sealed insulating plate, with each temperature zone's control area set flexibly.
4. ★ The reaction module has a three-layer structure, with the upper layer as the bottom plate, the middle layer as the mixing or reaction channel, and the lower layer as the heat exchange channel. The modules are made of silicon carbide material, and the forming process uses diffusion welding technology to ensure overall forming, gas tightness, and high-pressure resistance. To avoid metal leaching contamination, no metal connectors should be installed in the middle of the module.
5. ★ The reactor contains multiple sets of silicon carbide modules, including mixing modules and reaction modules, capable of executing A+B→P or A+B→P’+C→P. The mixing module can also be used as a quenching module for stopping the reaction or cooling down.
6. ★ The design of the reaction channel structure can enhance mass transfer while reducing back-mixing, ensuring the consistency of material residence time in the reactor, and requires the provision of internal structure diagrams.
7. Thermal conductivity: ≥100W/mK (within the temperature range of 200℃).
8. Corrosion resistance: The material in contact with the liquid in the reactor can withstand sulfuric acid, hydrofluoric acid, hydrobromic acid, strong alkalis, and other substances at the operating temperature of the reactor.
9. Annual loss rate: ≤0.1mm/year (tested under 120℃ 1:1 HF/HNO3 conditions).
10. Process side working temperature range: -20-150℃, heat exchange measurement temperature range: -20-150℃.
11. Process side pressure range: 0-25bar, test pressure 75bar, provide pressure testing certificate; heat exchange side pressure range 0-5bar.
12. Flux: 0.2-20mL/min.
13. ★ Internal volume of the reactor: 0.95-13.5ml, the minimum liquid holding capacity of a single plate shall not exceed 1ml, and the maximum liquid holding capacity of a single plate shall not exceed 4.8ml.
14. ★ The size of the reaction channel shall not exceed 1.4×1.4mm, and the size of the preheating channel shall not exceed 1×1mm.
15. Residence time: 2.7sec-60min.
16. Requirements for reactor accessories: The inlet and outlet pipelines and back pressure system must use corrosion-resistant and pressure-resistant materials to ensure the progress of gas-liquid reactions and liquid-liquid reactions.
Previous:
The next one:
Latest developments
Welcome your message consultation