Characteristics of Silicon Carbide Ceramics
2024-12-12
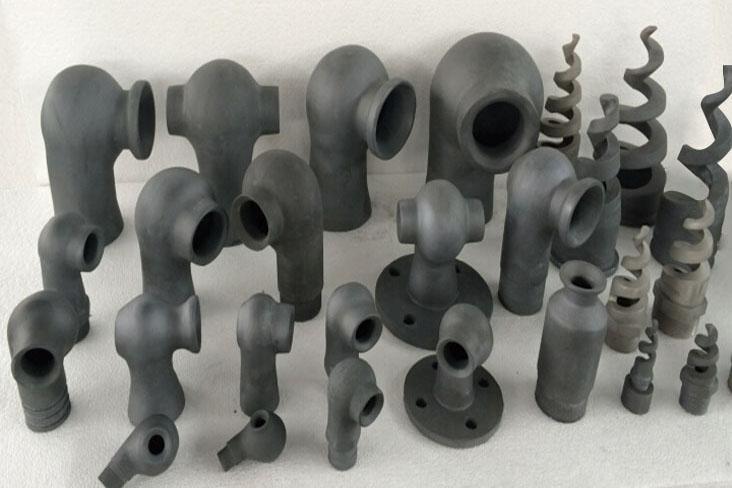
1. Pressureless Sintering: In 1974, GE in the United States successfully obtained high-density SiC ceramics at 2020°C using a pressureless sintering process by adding a small amount of B and C to high-purity β-SiC fine powder. This process has now become the main method for preparing SiC ceramics. More recently, researchers have added Al2O3 and Y2O3 to submicron SiC powder, achieving dense sintering of SiC at temperatures between 1850°C and 2000°C. Due to the lower sintering temperature and significantly refined microstructure, its strength and toughness have greatly improved.
2. Hot Pressing Sintering: In the mid-1950s, Norton Company in the United States began studying the effects of metal additives such as B, Ni, Cr, Fe, and Al on the hot pressing sintering of SiC. Experiments showed that Al and Fe are more effective additives for promoting the densification of SiC during hot pressing. Some researchers have used Al2O3 as an additive and achieved densification of SiC through hot pressing sintering, believing that the mechanism is liquid phase sintering. Additionally, other researchers have used B4C, B, or B with C, Al2O3 and C, Al2O3 and Y2O3, Be, B4C with C as additives, and also obtained dense SiC ceramics through hot pressing.
3. Hot Isostatic Pressing: In recent years, to further improve the mechanical properties of SiC ceramics, researchers have conducted studies on the hot isostatic pressing process for SiC ceramics. Researchers used B and C as additives and achieved high-density SiC sintered bodies at 1900°C using hot isostatic pressing. Furthermore, through this process, they successfully achieved the densification of additive-free SiC ceramics at 2000°C and 138MPa pressure. Studies have shown that when the particle size of SiC powder is less than 0.6μm, it can be densified at 1950°C through hot isostatic pressing even without introducing any additives.
4. Reactive Sintering: The reactive sintering method for SiC was successfully researched in the United States earlier. The process of reactive sintering involves first mixing α-SiC powder and graphite powder in proportion, and then forming a porous green body through dry pressing, extrusion, or casting. At high temperatures, the green body comes into contact with liquid Si, and the C in the body reacts with the infiltrating Si to generate β-SiC, which combines with α-SiC, while excess Si fills the pores, resulting in a dense, pore-free reactive sintered body. Reactive sintered SiC typically contains 8% free Si. Therefore, to ensure complete infiltration of Si, the green body should have sufficient porosity. Generally, appropriate green body density is achieved by adjusting the initial mixture's content of α-SiC and C, the particle size distribution of α-SiC, the shape and size of C, and the forming pressure.
Summary: Experiments have shown that SiC ceramics produced by pressureless sintering, hot pressing, hot isostatic pressing, and reactive sintering have different performance characteristics. In terms of sintering density and flexural strength, hot pressing and hot isostatic pressing SiC ceramics are relatively high, while reactive sintered SiC is relatively low. On the other hand, the mechanical properties of SiC ceramics also vary with different sintering additives. Pressureless sintering, hot pressing, and reactive sintered SiC ceramics have good resistance to strong acids and strong bases, but reactive sintered SiC ceramics have poor corrosion resistance to super strong acids like HF. In terms of high-temperature performance comparison, when the temperature is below 900°C, the strength of almost all SiC ceramics increases; when the temperature exceeds 1400°C, the flexural strength of reactive sintered SiC ceramics drops sharply. (This is due to the presence of a certain amount of free Si in the sintered body, which causes a sharp drop in flexural strength when the temperature exceeds a certain level.) For pressureless sintering and hot isostatic pressing SiC ceramics, their high-temperature performance is mainly affected by the type of additives.
The next one:
Latest developments