A Brief Discussion on Silicon Carbide
2024-12-12
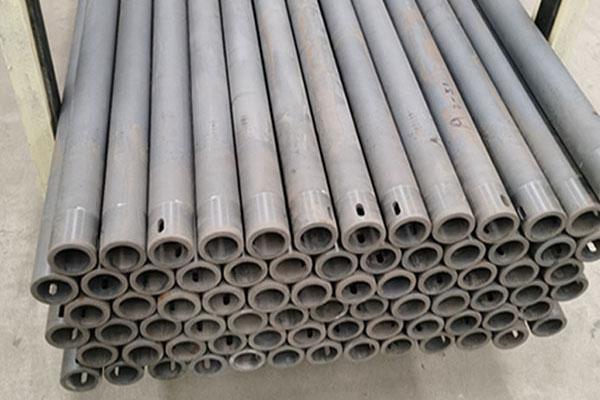
Silicon carbide, as a high-performance material, has received significant attention in the semiconductor industry in recent years. However, the applications of silicon carbide go far beyond this; it is not only used in the manufacture of power devices but is also widely applied in various fields as an abrasive, cutting tool, structural material, optical material, and catalyst support.
Silicon carbide ceramics possess a series of remarkable properties: stable chemical nature, high temperature resistance, wear resistance, corrosion resistance, high thermal conductivity, low thermal expansion coefficient, lightweight, and high mechanical strength. These characteristics make it an ideal material for many industries, including photovoltaic semiconductor equipment, lithium battery equipment, high-temperature industrial furnaces, chemical machinery, energy and environmental protection, metallurgy, national defense and military industry, as well as aerospace.
As a high-grade special ceramic, the hardness of silicon carbide ceramics is second only to diamond and boron carbide, with a Mohs hardness of up to 9.5, demonstrating excellent wear resistance. This makes silicon carbide ceramics very suitable for sliding components with high wear resistance requirements (such as mechanical seals, etc.). Its high Young's modulus and low thermal expansion coefficient also make it an ideal material for manufacturing high-precision components (such as optical components and substrates). Silicon carbide ceramics are high-density sintered bodies that can achieve mirror processing. They can withstand temperatures exceeding 1500°C, exhibiting excellent thermal shock resistance and chemical stability, making them suitable for manufacturing SiC suction cups, SiC sleeves, as well as thin and thick-walled products.
Silicon carbide composite ceramic materials are primarily composed of SiC and Si, formed after adding additives, and then placed in a nitriding furnace where high-purity nitrogen is introduced for nitriding sintering at a certain temperature. The preparation methods for silicon carbide ceramics include reaction sintering, recrystallization sintering, hot pressing sintering, and pressureless sintering, among others. Silicon carbide components for conductive equipment include water-cooled plates, suction cups, and crystal boats, characterized by high precision, high purity, and strong resistance to chemical and ionic corrosion. In the semiconductor field, the application of silicon carbide ceramics in industrial kilns has evolved from traditional industrial structural ceramics used in daily and sanitary ceramic kilns to various mid-to-high-end industrial structural ceramics used in new energy and semiconductor kilns.
In the future, as the penetration rates in fields such as new energy vehicles, energy, industry, and communications increase, and the demands for high precision, high wear resistance, and high reliability in mechanical components or electronic components become increasingly stringent, the market scale for silicon carbide ceramic products is expected to continue to expand, with new energy vehicles and photovoltaics being important development areas.
Previous:
The next one:
Latest developments